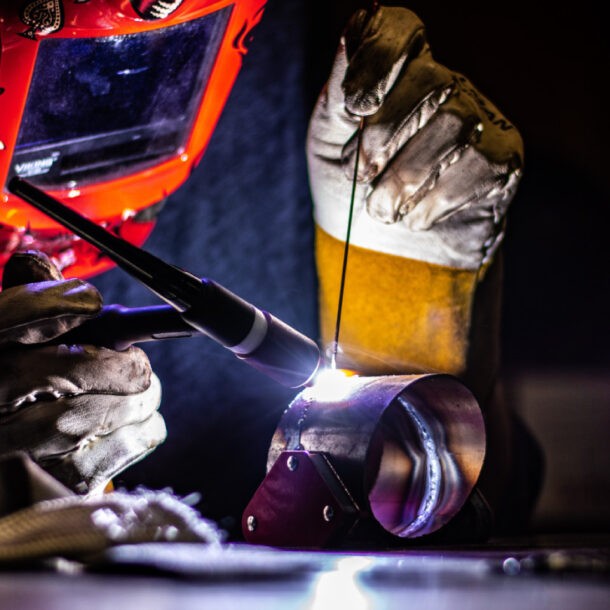
Se osserviamo con attenzione tutte le grandi strutture metalliche che ci circondano, noteremo che quasi tutte hanno almeno uno o più giunti saldati. Può sembrare difficile da credere, ma i vari processi di saldatura hanno richiesto molti secoli prima che divenissero efficaci. Allo stesso modo, la tecnologia necessaria all’esecuzione di saldature complesse ha richiesto non pochi anni di ricerca e sviluppo prima che le attuali e performanti macchine saldatrici venissero prodotte. Ad oggi è possibile, in funzione delle caratteristiche del giunto saldato richiesto, realizzare diverse tipologie di saldatura ed intervenire con tecniche che hanno reso fattibili lavorazioni che un tempo si pensava fossero impossibili da eseguire.
Le prime tecniche di saldatura risalgono ai tempi in cui il metallo stesso ha visto i suoi primi utilizzi da parte degli uomini. La “saldatura in forgia” ha segnato l’inizio di nuove tecniche di lavorazione e nuove opere realizzate. Fin dal medioevo le parti in ferro venivano unite al “calor rosso” sulla forgia e successivamente venivano martellate per poterle rendere omogenee. Solo nel 1901, mediante la saldatura ossiacetilenica, i procedimenti di saldatura cominciarono ad essere realmente riproducibili ed a restituire caratteristiche omogenee. Mediante questo procedimento, l’energia necessaria alla fusione delle parti era fornita dalla combustione di un gas (acetilene) con ossigeno puro. Grazie alle elevate temperature raggiunte non fu più necessario “martellare” le parti in modo da consentirne l’unione, rendendo l’operazione più semplice e soprattutto “ripetibile”.
Agli inizi del XX secolo vennero sviluppati generatori elettrici capaci di emettere un arco elettrico sufficientemente potente da fondere il ferro. Questa tecnologia segnò la nascita della saldatura ad elettrodo che tutt’oggi risulta essere la più diffusa al mondo.
Nel 1925 fu perfezionata la tecnica di saldatura a resistenza, utilizzata soprattutto in ambito industriale.
La necessità di produrre giunti saldati ad elevata resistenza, con produttività maggiore rispetto a quella ad elettrodo, decretò la nascita della saldatura a filo continuo (arco sommerso). Il procedimento fu di grande impego nel corso della seconda guerra mondiale.
Nel corso degli anni 50, con i procedimenti MIG e MAG, si ottenne una produttività equiparabile a quella ad arco sommerso con maggiore flessibilità di impiego. Contemporaneamente fu sviluppato il processo di saldatura TIG, che consentiva maggiore precisione durante l’esecuzione ed una lavorazione continua rispetto alla saldatura con elettrodo.
Negli anni 70, grazie alla ricerca ed allo sviluppo continuo, vennero introdotti i procedimenti ad energia concentrata (electron beam e laser). Questi procedimenti consentono di limitare con estrema precisione la zona di materiale modificata dalla saldatura.
Le principali tecniche di saldatura adoperate in ambito aeronautico possono essere distinte in:
Procedimento di saldatura ad arco con elettrodo infusibile (di tungsteno), sotto protezione di gas inerte, che può essere eseguito con o senza metallo di apporto. Questo tipo di saldatura fornisce giunti di elevata qualità e potrebbe sostituire l’installazione dei classici rivetti, garantendo parti molto più leggere a parità di resistenza.
La saldatura a resistenza è un metodo di saldatura autogena a pressione in cui il materiale viene riscaldato per resistenza elettrica. Questo tipo di saldatura consente di unire da due o più lamiere sovrapposte e presenta il vantaggio di avere una zona termicamente alterata sensibilmente più ridotta di quella di una saldatura ad arco
La brasatura consiste nel collegare pezzi metallici con l’ausilio di un metallo d’apporto senza la fusione dei pezzi da assemblare. Il metallo d’apporto penetra per capillarità all’interno dei pezzi da assemblare. Questo tipo di processo viene utilizzato quando i giunti sono costituiti da materiali difficilmente saldabili, quando i particolari sono costituiti da materiali metallici differenti e la loro saldatura è impossibile o quando l’aspetto estetico del giunto è di importanza prioritaria o indispensabile.
Tra tutte le tecniche utilizzate, compreso la costosa e rivoluzionaria saldatura laser, la diffusione della saldatura ad arco GTAW detiene ancora il primato grazie alla sua affidabilità ed ai suoi svariati campi di applicazione
Le diverse tipologie e tecniche di saldatura variano a seconda dello specifico campo di applicazione. Il settore aeronautico esige che i processi di saldatura, effettuati su leghe metalliche complesse, siano eseguiti in condizioni estremamente controllate.
La saldatura di materiali al titanio ad esempio viene eseguita “sotto vuoto” o in “atmosfera di gas protettivo totale”.
Tutti i processi di saldatura vengono quindi considerati “speciali” e richiedono qualificazione di impianto e degli operatori che eseguono i processi.
Specifici programmi di accreditamento, che prevedono iter di qualifica complessi, vengono seguiti al fine di garantire la qualità dei processi ed assicurano la corretta applicazione delle “best – pratices”.
Il costante e rapido progresso tecnologico consentirà, in un futuro non molto lontano, di utilizzare tecniche di saldatura sempre più performanti. Attualmente, oltre al perfezionamento delle tecniche di saldatura al plasma e laser, proseguono gli studi per la saldatura per diffusione.
Mediante questa tecnica il materiale da saldare non viene portato a fusione ma viene sottoposto a pressione. In questo modo, con temperature relativamente basse, gli atomi del reticolo cristallino diffondono attraverso la superficie di separazione dei pezzi realizzando il giunto saldato.
© 2021 AIRWIN - VIA CARLO POERIO 86 CAP 80121 (NA) - airwin@pec.it - REA NA 1042710 - P.IVA 09584381215 - Credits Made it srl